Revolutionizing Smart Warehouse Management: Introducing Smart Storage Racks and X-Ray Counter Machines
Revolutionizing Smart Warehouse Management: Introducing Smart Storage Racks and X-Ray Counter Machines
Introducing Smart Storage Racks and X-Ray Counter Machines
|
Paving the Way for Smart Material Management
With the advancement of industrial automation and smart manufacturing, many electronics manufacturers are striving to enhance the accuracy and efficiency of material management to remain competitive. Traditional warehouse management relies on manual operations, from material classification and storage to retrieval and distribution. These processes are often time-consuming and error-prone, leading to production delays or excess inventory, which in turn increases operational costs.
To overcome these challenges, we are introducing the X-Ray Counter Machine and integrating it into its Reel Management System. This transformation shifts material management from labor-intensive manual tasks into something smarter and more precise.
Additionally, the adoption of Smart Storage Racks has successfully resolved efficiency bottlenecks associated with traditional material access. This innovation provides the company with a more intuitive, faster, and streamlined operational experience, significantly enhancing productivity and reducing errors.
Smart Storage Racks: Simplifying Processes and Enhancing Efficiency
Each slot in the Smart Storage Rack is equipped with LED lights and sensors, combined with advanced technologies like barcode scanning, RFID, and the Internet of Things (IoT). These features provide real-time inventory visibility, with digital displays for warehouse managers. Seamlessly integrated with the ERP system, the Smart Storage Rack optimizes material storage and retrieval. During inbound storage, the system automatically suggests available slots and binds materials to specific locations using sensors. For outbound retrieval, the system activates LED indicators to quickly guide users to the required materials, reducing search time and errors.
This simple yet practical system offers real-time updates on slot status, material access guidance, and anomaly alerts. By enhancing accuracy and speed, it lightens the workload for warehouse staff while ensuring a smoother, smarter, and more efficient material management process.
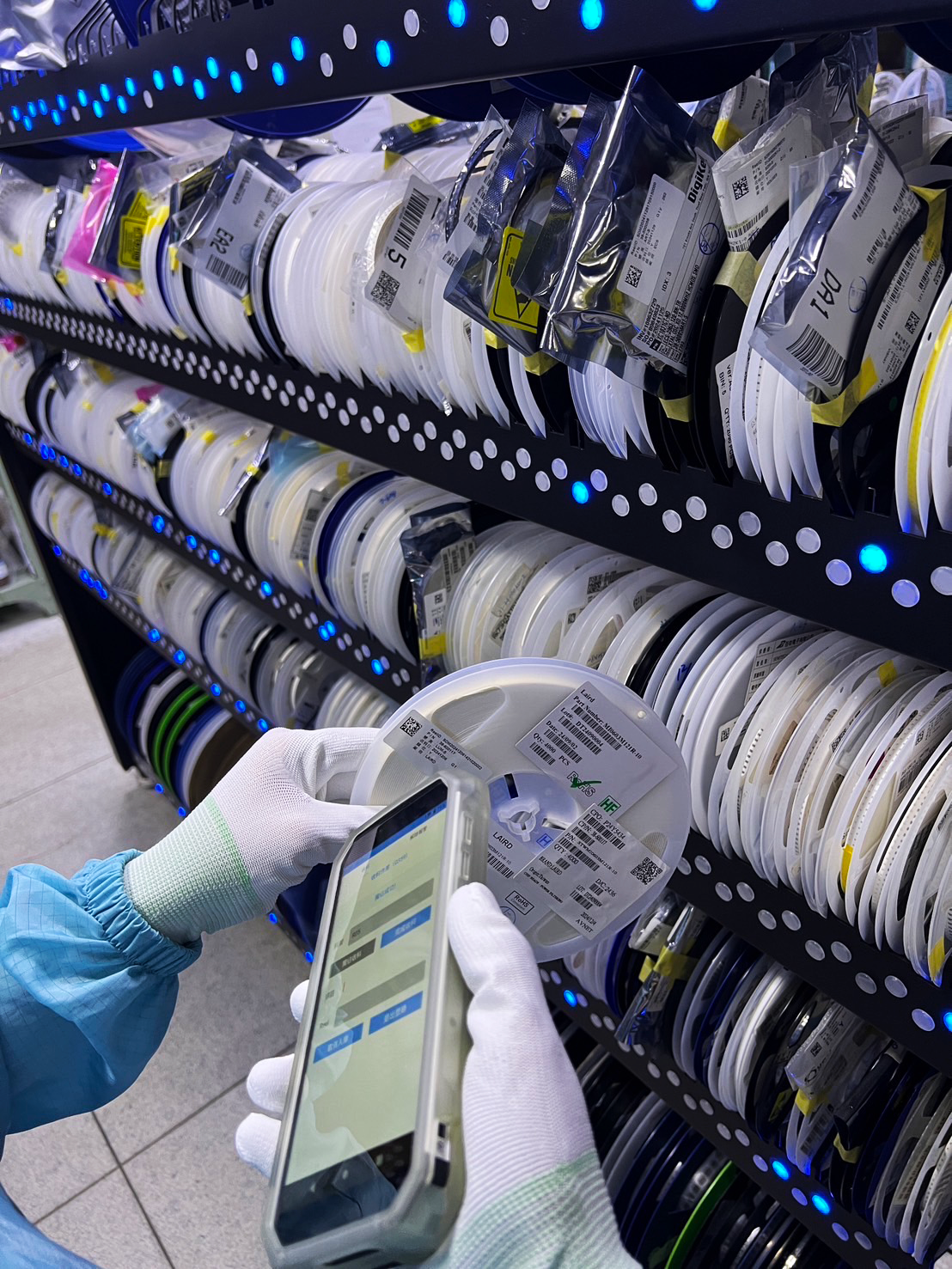
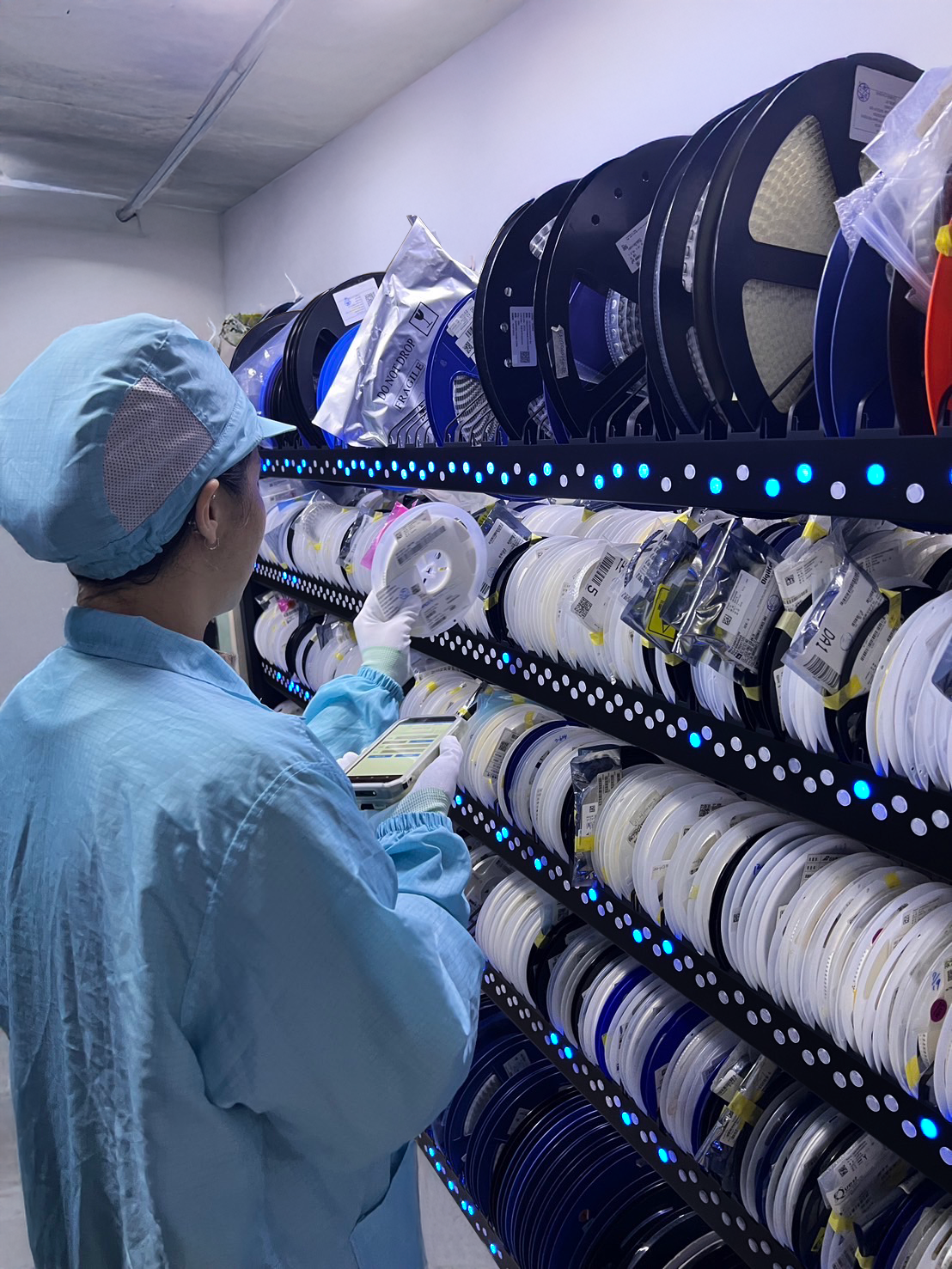
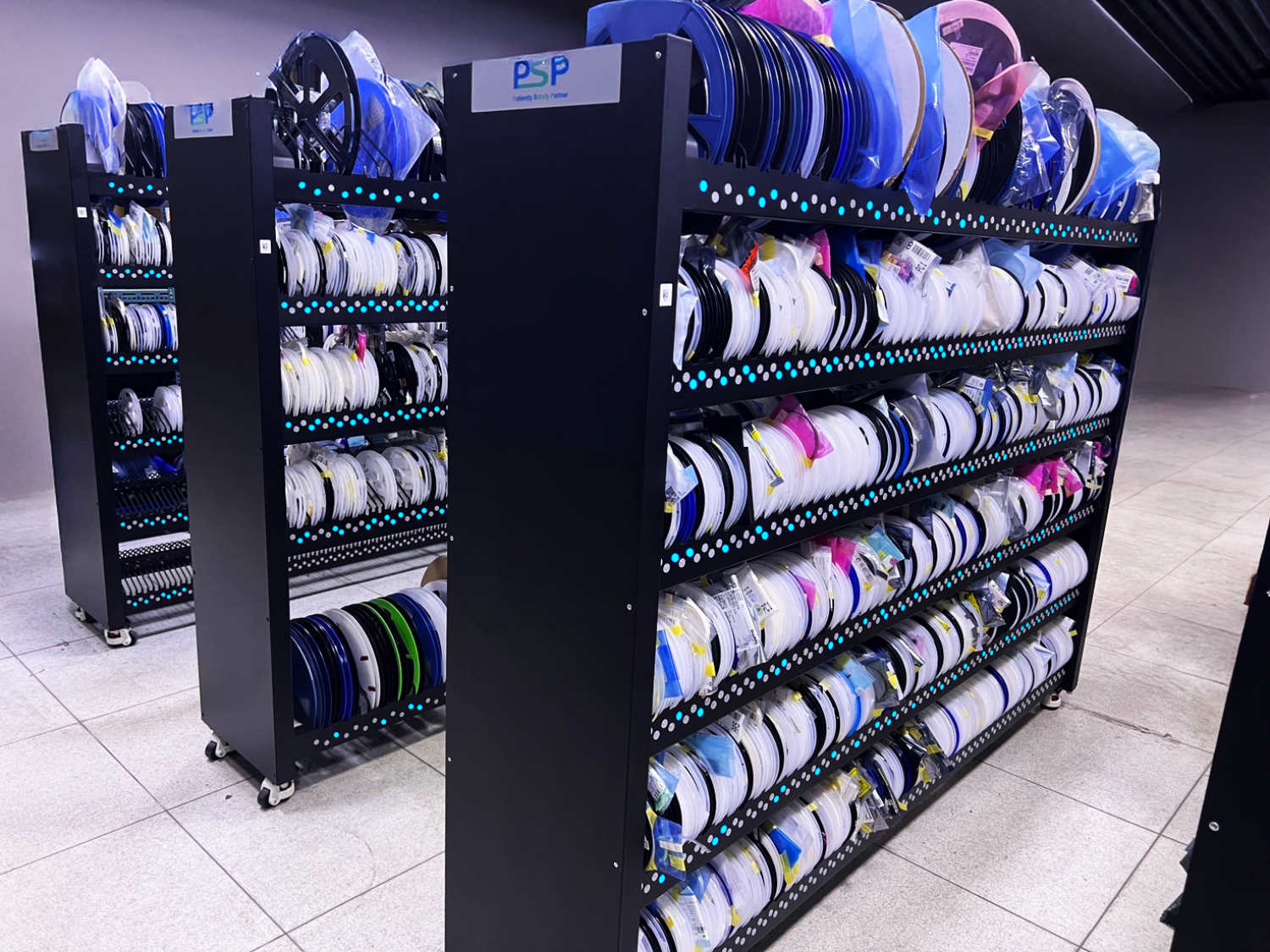
High-Efficiency Counting Technology: X-Ray Counter Machine × Smart Reel System
The X-Ray Counter Machine is a device based on the principle of X-ray penetration imaging. By utilizing non-destructive testing technology, it can quickly capture imaging information for production materials. Combined with AI-powered image recognition algorithms, the X-Ray Counter Machine can automatically calculate the actual quantity of materials and identify different types of components, ensuring data accuracy. Compared to manual counting, this technology offers significant advantages in both speed and precision. It not only reduces human errors but also shortens the overall material inspection time. This automated counting technology allows production lines to run more smoothly and prevents production delays caused by miscounts.
The integration of the X-Ray Counter Machine and the Smart Reel Management System brings highly coordinated workflow to enterprises. When new materials enter the warehouse, the system automatically generates a unique Reel ID and records the status of each material reel. During material issuance, the system guides warehouse personnel to retrieve the appropriate reel according to work order requirements and material issuance rules. Once the materials arrive at the production line, the X-Ray Counter Machine verifies the accuracy of the material count, ensuring precision. The verification records are automatically uploaded to the system, enabling real-time data updates. This level of automation not only significantly reduces manual complexity but also ensures the real-time flow of material information, improving traceability and operational efficiency.
After production is complete, production line personnel use the X-Ray Counter Machine to recount the remaining materials and attach a new quantity label. When warehouse personnel return the materials to storage, they only need to scan the Reel ID to automatically update the inventory data. This achieves real-time inventory tracking, saving a significant amount of time and reducing the risk of errors. This streamlined approach ensures efficient and accurate inventory management, supporting agile and flexible production operations.
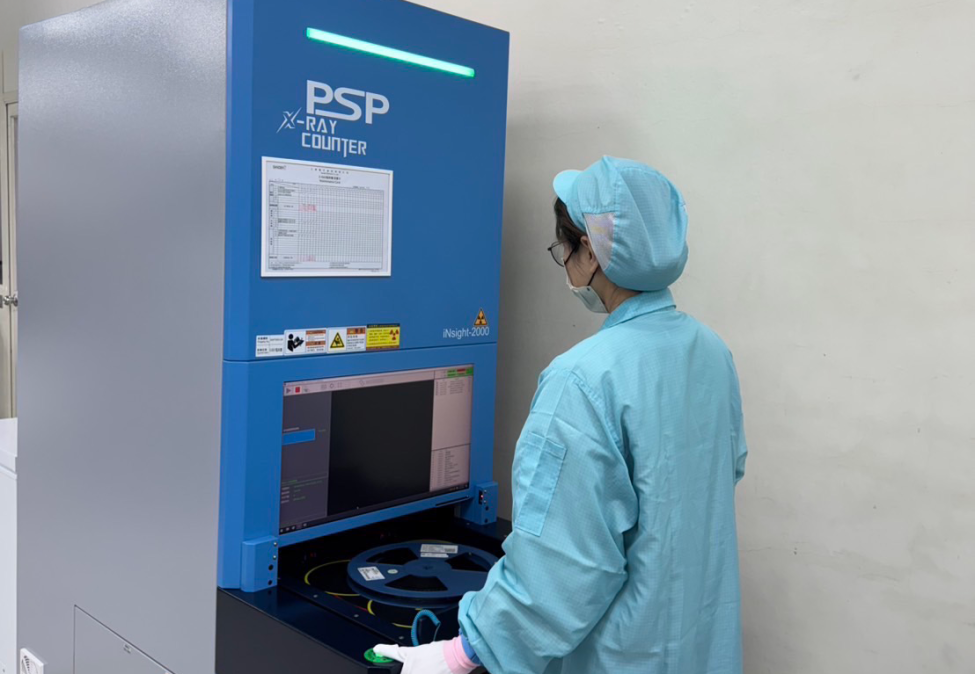
Future Outlook for Intelligent Material Management
With the continuous advancement of technology, warehouse management systems will continue to evolve. In the future, these systems will seamlessly integrate with more automated equipment and data analytics tools, enabling enterprises to achieve even more refined and agile material management.
We are committed to creating a stable and reliable production environment, driving the manufacturing industry toward a more efficient and intelligent future.